Share
Pin
Tweet
Send
Share
Send
It was decided to make the next new bench as non-metallic as possible. The maximum task was such that the only metal part of the finished product was nails and screws.

By the way, the budget implied only the costs of those same consumables, and all the materials were found in the yard and sheds. Now, first things first.
Preparation of materials and tools
For work, not many tools were needed: a hammer, tape measure, level, tongs, pliers, a saw, a grinder (you can do with a metal blade), a screwdriver and an ax.
The materials were found somehow by themselves. Old window pieces came up for the legs (the impressive thickness and density of the tree is just in time).

Boards with a thickness of about 20 mm went to the seat (made in USSR, like loot, so there are no questions about the quality at all).

It would be possible to leave the surface wooden and paint, but the remains of plastic lying around idle literally radiated a desire to be useful.
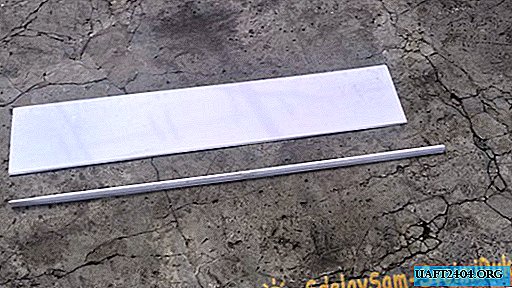
The expected height of the legs was to be 45 cm, so the remaining 55 cm of the tree went for treatment with waste machine oil.
Seat assembly
Two boards in total gave a width of 26 cm, which was enough for the head. It remains to slightly trim the tree and successfully combine the two parts together. Considering that the boards were not the first freshness and were originally intended for rough work, I had to tinker with the connection to avoid height differences.

A little nerves, four nails, and you're done.

The plastic profile, creating a kind of rails for a piece of plastic, was fixed on the self-tapping screws, "bugs" around the perimeter of the seat. One of the smaller sides will need to be fixed after the installation of the bench.

It turned out very well. Thanks to careful measurements and even trimming, the plastic perfectly fell into place.

The finished seat looks like this.

Installation
Again, due to a modest budget and unwillingness to go to the store for cement, it was decided to set up a shop without unnecessary expenses.
A pair of pits dug up unexpectedly easily, and the most difficult was to level the legs so that in the end the bench did not warp. The rammed earth and broken brick gave exactly the effect that was needed. Even when only half the pit was filled, the shop was already standing very, very confident. When the pits were completely abandoned, it turned out somehow. It only remained to nail the seat to the legs.

Checked three together: a total of about 200 kg withstood. The legs will be painted a little later, but for now I’d like to write on white plastic that there is no metal in this shop, and you don’t need to try to get it out of the ground.
Share
Pin
Tweet
Send
Share
Send